Recent advances in the sustainable aviation industry
Air traffic doubles every 15 years, with an 80% increase in the number of flights between 1990 and 20142.
With that being said, global aviation emissions are projected to grow by 300-700% compared to 2005 levels3, driving the urgency to implement more environmentally sustainable technologies into the aviation system.
Increased interest in this effort is motivated by the impact of burning fossil fuels, which includes natural resource depletion as well as climate change.
In addition, the aviation sector is concerned by rising oil prices and dependence on suppliers.
Thus, researchers all over the world are scrambling to figure out a more secure way to fuel aviation and mitigate its carbon footprint.
Accordingly, US airlines have achieved an improved efficiency of 130% compared to 19784.
However, despite immense improvements in aircraft technology, the industry has only been able to reduce carbon emissions by less than 15%.
Although there are possible improvements to be made in turbofan engines for the purpose of decreasing emissions, it is clear to many experts that decoupling carbon growth will require the implementation of aviation fuel which is not derived from petroleum. Jet engine design evolution generally takes 14 to 19 years to complete and is
extremely expensive, costing hundreds of millions of dollars, in comparison to the process of fuel certification, which generally takes three to five years and costs $5 million (€4.2 million) to 15 million (€12.6 million).Furthermore, non-liquid fuel technologies like electrification or fuel cells do not currently have the sufficient energy density to run a commercial aircraft4,5. Figure 1 displays a comparison of various potential energy sources for aviation.
New approach
A more feasible approach to this issue will be to implement drop-in sustainable aviation fuel (SAF) into the current aircraft infrastructure.
According to the International Civil Aviation Organisation (ICAO), SAFs are defined as alternative aviation fuels which achieve net GHG emission reduction
throughout the life-cycle, respect biodiversity, contribute to social and economic development, and avoid competition with food and water supply.
With airlines committed to reducing their carbon footprint by 50% before 2050 there is a clear need to begin the process of implementation.
That is why United Airlines began using alternative fuels in 2016, and Delta Airlines currently plans for 10% of its fuel to be SAF by the end of 2030.
Studies suggest the use of SAFs as a replacement for conventional fuel has the potential to reduce GHG emissions by 55-92% compared to 2005 levels.
Thus, this approach is more promising in the near term than any other, and it is already underway.
In October 2016, the ICAO announced the Carbon Offsetting and Reduction Scheme for International Aviation (CORSIA), which aims at offsetting 80% of harmful emissions above 2020 levels. The plan involves a proposed timeline for implementation and transition.
There will be three phases: Phase I will take place during the years 2021-2023, Phase II will be during 2024-2027, and Phase III will be from 2028-2035.
Phases I and II are known as the voluntary phases, in which airlines may choose to participate, whereas Phase III will involve obligatory mandates which will be enforced by requiring extra payment for producing excess carbon emissions above 2020 levels for all international flights.
To meet the ICAO goals, over 30% of global jet fuel consumption will need to be SAF by 20404.
Jet fuels consist of four families of hydrocarbons: n-alkanes, iso-alkanes, cycloalkanes, and aromatics. Other molecular families such as oxygenated molecules, heteroatom-containing molecules, unsaturated hydrocarbons (olefins), and metals are unsuitable.
This may be due to varying reasons which include poor thermal stability, freeze point, and specific energy.
The bulk properties of jet fuel are mainly determined by the hydrocarbon class composition. Important performance properties include specific energy, energy density, emissions, and thermal stability. Safety and operability limits areprimarily shaped by the viscosity, density, surface tension, flash point, and reactivity (DCN) of a fuel.
Additionally, a low freeze point is a key property among jet fuels, for it allows long range flights to use more optimum flight profiles.
These properties essentially determine the range, payload, and cycle efficiency of a jet fuel in use. Table 1 outlines each of these properties and their relevance.
Improvements to the specific energy can enable more passengers and cargo by reducing the weight of the aircraft during flight.
Therefore, when formulating alternative jet fuels, there is an opportunity to not only substitute but outperform traditional fuels by producing a hydrocarbon mixture of maximum desirability while maintaining drop-in compatibility.
The n- and iso-alkane classes generally compose about 55-60% of conventional jet fuel. These molecules tend to have high specific energy, low energy density, and high thermal stability in relation to others.
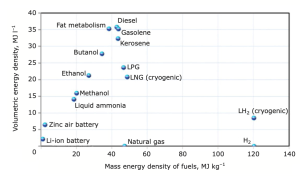
However, despite having the highest DCN among similar hydrocarbons, n-alkanes are known to have poor jet fuelcharacteristics, for larger versions have high freeze points while smaller versions do not meet the required flash point. Therefore, the blend potentials of n-alkanes are limited. In contrast, iso-alkanes have low freeze points and demonstrate desirable jet fuel properties,
though they are expensive and require continued research and development toward reducing their cost.
SAF alternatives The hydrocarbon family of cycloalkanes includes a diverse spectrum of molecules. Average Jet A fuel is composed of monocyclic and fused bicyclic molecules.
Monocyclic alkanes can portray a density, specific energy, freeze point, and flash point which exceed the necessary requirements.
Different subclasses of cycloalkane molecules have varying properties and remain an area of exploration within this field.
These molecules are necessary in jet fuel to ensure the swelling of seals to prevent fuel leaks (this only applies to seals which have previously been exposed to fuel).
However, aromatics have been labeled as the most significant contributor toward soot and particulate matter emissions, being responsible for up to 90%. Owing to the fact that these molecules do not burn cleanly, environmental benefits have been realised with fuels containing a low aromatic content.
SAFs with low aromatic content have been reported to reduce soot formation and other emissions by 50-70%. Since drop-in SAFs are blended with petroleum fuel containing adequate amounts of aromatics for swelling, there is little need for renewable fuels to continue to contain these molecules. Table 2 shows a breakdown of the bestcase, average, and worstcase composition makeup and properties in jet fuel.
Putting things into perspective, out of the four hydrocarbon groups, the two most important for researchers to look into are iso-alkanes and cycloalkanes.
Iso-alkanes are necessary for specific energy, while cycloalkanes provide sufficient energy density. Aromatics show the least desirable characteristics
and are, therefore, limited to 20% capacity. Research has shown opportunities to produce an attractive fuel in which aromatics are diluted with renewable iso-alkanes initially, to then be fully replaced by cycloalkanes.
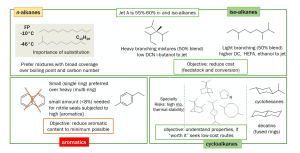
A SAF containing a mixture of cycloalkanes and isoalkanes could increase energy density and specific energy, as well as meet the other performance characteristic requirements such as freeze point, flash point, swelling demands, and low emissions.
Figure 2 summarises a strategic outlook on the four hydrocarbon families.
Common feedstocks include municipal solid waste, cellulosic waste, used cooking oil, or plants such as camelina, jatropha, halophytes, or algae.
There are also nonbiological alternative fuels such as what is known as power-to-liquid jet fuel.
Some alternative jet fuels are currently approved for flight by ASTM D7566 in blends with traditional kerosene of up to 50%. ASTM D7566 is the Standard Specification for Aviation Turbine Fuel Containing Synthesized Hydrocarbons. Any fuel intended to be put to commercial use must be certified by ASTM International first, undergoing a long process of testing. As of 2020, there have been eight pathways approved by ASTM for the production of SAFs.
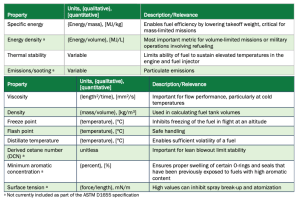
Seven annexes to D7566 are outlined in Table 3. In addition, ASTM D1655-20b (as of 2020) permits co-processing as a means of converting fats, oils, and greases from petroleum refining into jet fuel for a blending limit of up to 5%. Fischer-Tropsch Synthetic Paraffinic Kerosene (FTSPK) is the earliest SAF to be approved by ASTM. This fuel is a mixture of iso- and n-alkanes and can also be called syngas. The production process involves gasification with Fischer-Tropsch synthesis, which transforms either lignocellulosic biomass or solid waste into fuels.
The main feedstocks are different types of biomass, including wood waste, grass, or municipal solid waste. Key steps include feedstock pretreatment, gasification, syngas conditioning, Fischer-Tropsch catalysis, distillation, and hydrocracking, with the possible addition of isomerisation and catalytic reforming. This fuel can be applied to turbofan engines in blends with traditional petroleum fuel of up to 50%4. FT-SPK can also be produced through a power-to-liquid (PtL) process in which carbon and hydrogen are catalytically combined via electrolysis. Electricity, water, and a concentrated source of CO2 are required for this operation. Costs for this route can be very high depending on the electrical cost.
However, PtL is currently attracting widespread interest due to its ability to produce fuels with low GHG emissions without the involvement of biomass feedstock constraints.
Hydroprocessed Esters and Fatty Acids (HEFA-SPK) is the most commercially mature route. It has a similar molecular composition as FT-SPK, consisting of iso- and n-alkanes.
It is produced by the hydrotreating of esters and fatty acids from fats, oils, or greases derived from feedstocks such as algae, jatropha and camelina.
Hydrogen is utilised to convert unsaturated compounds like alkenes and aromatics into more stable molecules like cycloalkanes and paraffins.
The energy conversion efficiency for this route is about 76%, which is the highest efficiency among approved biojet fuel technologies.
In addition, the lowest alternative fuel costs are associated with this pathway in terms of hydroprocessing used cooking oils or animal fats. This fuel can be applied in blends of up to 50%.
Unlike the others, Hydroprocessed Fermented Sugars to Synthetic Isoparaffins (HFS-SIP) is made up of a single molecule, which is a 15-carbon hydrotreated sesquiterpene known as farnesane.
Farnesane is produced by the fermentation of sugars, which is done commercially from sugar cane juice.
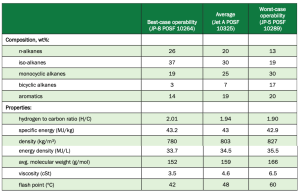
However, this fuel is limited to blends of up to 10%. The process involved in converting lignocellulosic sugars into fuels causes this to be the most expensive alternative fuel pathway due to its complexity and low efficiency.
FT-SPK with aromatics (FT-SPK / A) is essentially the same as the first approved SAF, with the addition of aromatics in the molecular composition.
The feedstocks are the same as well, that being renewable biomass such as municipal solid waste, and agricultural and wood waste. This fuel can be blended up to 50% for direct application.
Alcohol-to-jet Synthetic Paraffinic Kerosene (ATJ-SPK) is currently approved for SPK from iso-butanol for up to 30% blends as well as from ethanol for up to 50% blends. This fuel consists of iso-alkanes of 8, 12, or 16 carbons when starting from iso-butanol. When starting from ethanol, the carbon number can be broadened and the branching level can be reduced.
Feedstocks for the production of alcohol include agricultural waste like corn shoots, grass, and straw, or cellulosic biomass . The alcohols are then turned into jet fuel through the processes of dehydration, oligomerisation, hydrogenation, isomerisation, and distillation. The highest reduction in GHG emissions for the ATJ route can be achieved by using iso-butanol derived from forest residues, yielding an outstanding reduction of 74%.
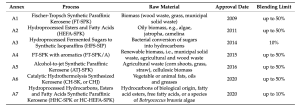
Catalytic Hydrothermolysis Synthesised Kerosene (CHSK or CHJ) is produced from lipids derived from vegetable or animal fats.
This fuel contains all four hydrocarbon families, including n-, iso-, and cycloalkanes, as well as aromatics.
The lipids are converted into jet fuel using a supercritical hydrothermal process, to then be blended with petroleum fuel in up to 50% composition.
Hydroprocessed Hydrocarbons, Esters and Fatty Acids Synthetic Paraffinic Kerosene (HHCSPK or HC-HEFA-SPK) is made from lipids derived from a specific species of algae called Botryococcusbraunia that have undergone hydrocracking/hydroisomerisation to remove oxygen and saturate double
bonds. The product of this process is rich in iso-alkanes.
This pathway was the first to be approved through the ASTM D7566 ‘fast track’ process, but it is limited to blends of up to 10%. ASTM D1655-20b allows the co-processing of mono, di-, and triglycerides, as well as free fatty acids
and fatty acid esters of up to 5% FT hydrocarbons.
Hydrocracking/hydrotreating and fractionation are required for this process. Thus far, coprocessing in refineries is not permitted for jet fuel besides
this one pathway. Before reaching the D7566, fuels must make it past
the ASTM D4054 approval process. Currently, several fuels are caught in the D4054 approval pipeline, waiting to be streamed into D7566 approval. This includes SPK ( and iso-alkanes), cycloalkanes, aromatics, and mixtures of all four hydrocarbon families.
The 106 billion-gallon global market is projected to reach over 230 billion gallons by 2050. With biomass as the main SAF feedstock, there is currently about 340 million tons of biomass available in the US. This could amount to roughly 21 billion gallons of jet fuel, which just about matches the domestic
market size4. However, the aviation fuel industry must compete with other feedstockdemanding markets such as ethanol and biodiesel.
Current policies are focusing renewable fuels toward diesel and the much larger, more demanding motor-vehicle industry. In 2014, there were around 1.2 billion vehicles on the road compared to only 26,000 commercial aircrafts in flight.
This demonstrates the unbalanced market sizes and gives reason to why there may be a skew in the raw material demand. However, this also means that integrating alternative fuels into the aviation industry could potentially be a lot easier due to its small size and centralised nature.
To prevent diesel and ethanol production from cornering the biomass supply, appropriate policies should be placed so as not to skew the focus.
Another notable barrier in the widespread application of SAF is that alternative fuels are significantly more expensive in comparison to traditional Jet A fuel.
To demonstrate, the cost of SAF range from two to five times the price of fossil kerosene7. Considering that fuel makes up 20-30% of aviation operating costs,
this will be a problem for the industry. As it is, airlines are expected to pay 40% more for jet fuel by 2040 compared to what they paid in 20145. For SAF to scale, prices need to be reduced through research and development.
Additionally, since this approach does not require land to produce the feedstock, there are less sustainability concerns. For instance, the land use in the production of biomass feedstock, as well as the hydrogen and other inputs necessary during the conversion processes of biojet fuel generate carbon emissions which need to be considered.
However, these concerns can be diminished when taking into account the lifecycle basis in which excess carbon produced is recycled through the
biomass via photosynthesis.
The amount of CO2 absorbed by plants is similar to the amount emitted during the combustion of biofuel. In this way, remaining neutral in terms of GHG emissions is much easier in comparison to the use of conventional jet fuel2, for these biofuels can reduce lifecycle emissions by 20-95%. Therefore, waste material and raw biomass are both attractive feedstocks, but cost is still a concern.
Although research needs to focus on reducing the price of SAF, there is hope for its current economic viability.
For more information:
This article was written by Dr Raj Shah, a director at Koehler Instrument
Company, and Eliana Matsil, a student of chemical engineering at SUNY, Stony Brook University, Visit: koehlerinstrument.com.