A proven biofuels asset
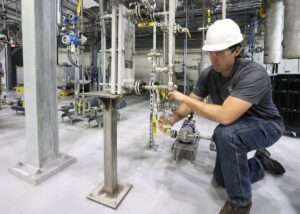
The Global Innovation Centre has been instrumental in both client and internal innovations for process and equipment designs.
The products and processes have varied considerably, from traditional oilseeds to new-to-the-world oilseed crops, but the biggest areas of interest have been in plant-based proteins and pretreatment of feedstocks for biofuels.
Pilot plant
The pilot plant is a smallscale continuous production facility, built to mimic full-size equipment and processes in nearly every detail. It operates 24 hours per day and includes a control room and laboratory like one might find at a processing plant.
Oilseeds and other raw materials are processed into final products and any intermediates or co-products relevant to the project. In 2022, Crown’s Liquids Pilot Plant was added to the Global Innovation Centre with capabilities to pretreat oils and fats to the specifications for RD and SAF feedstock.
This investment by CPM and Crown represents a significant commitment to the biofuels industry and creates the opportunity to bring in novel oilseeds and take them all the way to pretreated feedstocks for renewable fuels. In addition, the company recently finished the installation, commissioning and first operations of a 31-metretall processing tower with capabilities for fat splitting, edible oil deodorisation and methyl ester and fatty acids distillation. In an ironic twist, many biofuel producers have so far used the pilot plant more to explore co-products other than the resulting oil.
In many cases, these clients intend to produce vegetable oils for biofuels, but they also have to develop end markets for these co-products.
They are provided with product samples for that purpose. They may also need validation of the processes to justify investments in new processes and facilities.
In most cases, piloting begins with bench scale testing and analysis. These smaller volumes allow quicker responses and give an indication of the value of full pilot testing.
The results from testing a few litres in the laboratory also lead to better planning for a full pilot run. The lab testing and analysis continues even after the pilot run begins.
In one interesting situation, a client proposed a standard approach to pretreatment, which seemed to make sense given the feedstock. However, during the operation, the lab analysis did not match expectations created during bench scale testing.
Engineers quickly changed the sequence of the unit operations to try something unique.
The results spoke for themselves as it was quality expectations through a modified process. Recently, when a client was looking for mitigation of specific parameters in their feedstock, CPM’s Crown was able to modify and install new equipment and then test the performance of those changes all before finalising the pilot run for that feedstock. As new issues arise in the marketplace, Crown is able to adapt and adjust.
Feedstocks
SAF and renewable fuels producers are always concerned with feedstocks. Many of the most interesting feedstocks have limited availability and questionable quality.
Even when a certificate of analysis is provided, there is still risk that the delivered material will not match expectations because quality can vary quite a bit.
The company has seen these differences between the small volumes for bench testing and the larger quantities that arrive for pilot testing. The pilot plant can be a great environment for learning about feedstock quality variations. For these situations and many others, it may make sense to run a pilot test for risk mitigation.
The Global Innovation Centre also provides an excellent opportunity to train people on the exact processes found in full-size pretreatment plants. Control board operators, supervisors and even process engineers will find value in seeing this equipment firsthand, learning how feedstocks move through pretreatment, and how each step is controlled and monitored.
For more information: Visit: crowniron.com/biofuel
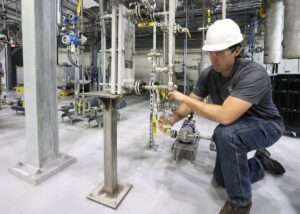