Made from non-petroleum feedstocks, SAF is vital in reducing the aviation industry’s carbon footprint.
Many countries, universities, research labs, and companies are actively researching and investing in developing new feedstocks and production pathways to make SAF production more sustainable and cost-effective. The availability of raw materials can vary regionally, and SAF production often involves a combination of feedstocks to meet demand.
Introduction
In recent years, the global aviation industry has experienced rapid expansion, with a heightened emphasis on sustainability, particularly in using SAF. Notably, significant strides have been made in SAF production, involving the scaling up of production facilities. Numerous companies and governments have invested in expanding SAF production capacity to meet the escalating demand from airlines.
SAFs play a crucial role in commercial aviation, potentially reducing carbon dioxide emissions by 80% [1].
These fuels can be derived from various feedstocks or synthetically produced, utilizing carbon captured directly from the air. Examples of suitable feedstocks include oil seed plants, algae, municipal solid waste, fats, oils, greases from cooking waste, agricultural and forestry residue, as well as industrial carbon monoxide waste gas. SAFs contribute to carbon dioxide recycling by utilising biomass that absorbs carbon during its life cycle.
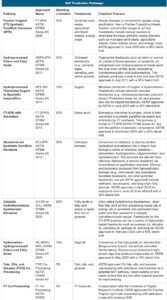
The surge in air traffic demands has consequently increased the need for aviation fuel. Annually, approximately 80 billion gallons of jet fuel, classified as kerosene-type and naphtha-type, are produced globally. The extensive reliance on petroleum-derived jet fuel has led to a significant decline in petroleum reserves. Furthermore, the substantial consumption of jet fuel contributes significantly to greenhouse gas emissions, making the airline sector accountable for 3% of the total current GHG emissions [2].
Production process
The production of SAF is initiated from one of five primary families of raw materials: oils and fats, sugar and cereal, municipal solid waste, wood and agricultural residue, or renewable energy and carbon. Each feedstock employs a specific production technology, and every technology pathway requires approval from the fuel standard body ASTM before commercial deployment. Figure 1 outlines these pathways and their associated ASTM approvals.
SAF production is broadly categorized into standalone units or co-processing. Standalone units utilise sustainable feedstocks to produce synthetic kerosene (SK), blended with conventional jet fuel to create SAF. Conversely, in co-processing, up to 5% of sustainable feedstocks undergo hydro-processing alongside fossil feedstocks in the refinery [3].
As mentioned earlier, SAF can be derived from non-petroleum-based renewable feedstocks, including the food and yard waste portion of municipal solid waste, woody biomass, fats/greases/oils, and other sources. The Environmental Protection Agency (EPA) collects renewable fuel data through the Renewable Fuel Standard, offering an approximate consumption estimate for novel biofuels like SAF. EPA data indicates around 5 million gallons of SAF were consumed in 2021, increasing to over 14 million gallons in 2022 (through November). Anticipated growth in production is expected in the coming years, with many domestic and international airlines signing agreements with existing and future SAF producers to utilize hundreds of millions of gallons of these fuels [4]. Various technological pathways for fuel production are illustrated in Figure 1.
Current status and perspectives on fully synthesised SAF
The U.S. Department of Energy issued a “Grand Challenge” to increase sustainable jet fuel production to 3 billion gallons per year by 2030 to reduce aviation greenhouse gas emissions. Its goal is to produce enough fuel to meet 100% of commercial jet fuel demand by 2050 [4]. SAF production and use in the U.S. has increased in recent years; however, the usage of SAF is limited to airlines at two major commercial airports in California. While U.S. production has grown to 15.8 million gallons in 2022, as shown in Figure 2, it accounted for less than 0.1 percent of the total jet fuel used by major U.S. airlines [6].
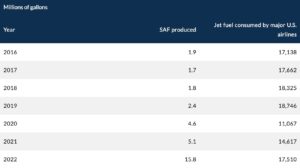
Figure 2: Comparison of Sustainable Aviation Fuel (SAF) Produced and Jet Fuel Consumed by Major U.S. Airlines by Year [6].
If the production of SAF continues this grow at the current rates, there is potential for SAF to provide the bulk of the emissions reductions the industry will need to make by 2050.
Figure 3: Contribution to achieving net zero by 2050 [7]
The state of SAF in 2023 includes over 130 renewable fuel projects, seven technical pathways, over 300 million liters of SAF production, and usage in more than 490,000 flights [7]. Current SAF results in a 70% average carbon dioxide reduction compared to traditional kerosene.
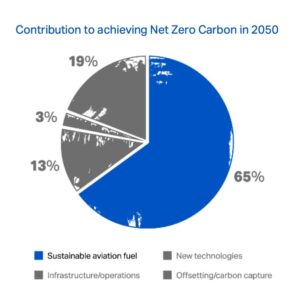
To lower greenhouse gas (GHG) emissions, the aviation industry has announced "zero-emission" plans and goals from manufacturers and carriers. Achieving these objectives depends on further reducing the carbon dioxide associated with SAF and substantially increasing its usage. To increase the usage of SAF, it is required to have similar properties to current jet fuel, such that they can be blended [8]. Eventually, the aviation sector seeks to move toward using 100% synthesized aviation fuels that also meet sustainability criteria.
By facilitating the use of alternative jet fuels in the aviation industry, the Commercial Aviation Alternative Fuels Initiative (CAAFI), a public-private partnership comprising the US government, aviation industry stakeholders, and aviation fuel supply chain participants, has been working since 2006 to improve energy security and environmental sustainability for aviation.
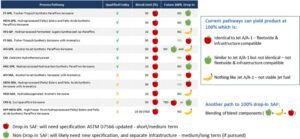
Initially, the industry and CAAFI concentrated on qualifying synthetic fuel blending components that originate from non-petroleum sources to be added to conventional aviation fuel sourced from petroleum, which is qualified by ASTM D4054 for use in ASTM D7566 (see Figure 4) because of safety and compatibility concerns. To guarantee that the attributes of all blended fuels fall within approved ranges for Jet, specific blending components are restricted to a maximum blend percentage [8].
Fig 4: Types of synthesized fuel blendstocks and their ability to be used as drop-in fuels as blendstocks or as stand-alone fuel. The red apples indicate fuels that can be drop-in, green apples are similar to drop-ins and may be usable in some existing aircraft but would require modification of the existing specifications and possibly infrastructure, and bananas indicate fuels that are completely different from petroleum-based kerosene and could not be used as stand-alone jet fuel in current infrastructure or equipment [8].
Some approaches to achieve 100% synthesised jet fuel are to Replicate all Jet A/A-1 properties in a single fuel, replicate all Jet A/A-1 properties in blended fuel, substitute for aromatics or reduce aromatics requirement, remove the requirement for seal-swelling components (non-drop-in) and redefine jet fuel requirements. The first two alternatives are 100% synthetic fuels made from a single or a combination of fuels and might be feasible soon. Still, options 3 and 5, which redefine the need for jet fuel depending on additional research, might be viable if enough time and knowledge are gathered. Option 4 (non-drop-in fuels) is not preferred since it would necessitate large-scale, costly modifications to the infrastructure and equipment of aircraft.
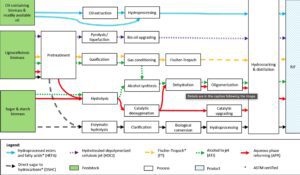
To further refine the definition of a 100% synthesized aviation fuel to 100% Sustainable Aviation Fuel, any SAF needs to be produced in a way that demonstrably meets sustainability criteria to ensure environmental, social, and economic performance. Sustainability requirements are applied to synthesized aviation fuels separately from the technical, safety, and performance characteristics that qualify a fuel to be used in aviation under the ASTM specifications; therefore, a 100% synthesized fuel is not necessarily a 100% sustainable aviation fuel even if it comes from a renewable feedstock. Nevertheless, the sustainability performance is critical to the value proposition of these fuels and must be ensured.
Commercialisation
Currently, 2% of the world's anthropogenic carbon emissions come from aviation. It is projected that as demand increases, annual carbon dioxide emissions will rise quickly, from 705 Mt in 2013 to between 1000 and 3100 Mt by 2050 [9]. The aviation industry must significantly cut its specific carbon dioxide emissions per passenger kilometer to support global policy goals to prevent climate change. However, there are few choices available soon to decarbonize air travel.
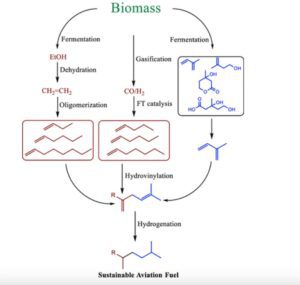
Modern airplanes' fuel efficiency is already great, and technological advancements are usually gradual.
Furthermore, because commercial aircraft have a 25-year service life, improvements are anticipated to spread slowly throughout the active worldwide fleet. Aviation emissions could be reduced by an estimated 0.8% annually from 2015 to 2050 due to improved air traffic control and engine efficiency [9]. However, these reductions are not anticipated to be large enough to counteract increases in passenger volume. Adopting low-carbon liquid fuels, especially biofuels, is necessary to achieve most of the emission reductions.
To gain a comprehensive understanding of the current and projected facilities for Renewable Jet Fuel (RJF) production and to identify the political and economic factors influencing RJF deployment in the future, we employed a Rapid Evidence Assessment (REA) approach. REA is a strategy that utilizes best practice systematic review procedures for evidence-based policy. It involves a thorough literature search to address a specific research issue, aiming to gather and synthesize evidence while minimizing bias in paper selection. However, it is important to note that this method has a drawback – it may potentially miss publications that do not fit the specified search parameters.
Technical certification by the American Society for Testing and Materials is one of the most significant steps toward a new fuel's commercial acceptability. The scope of the REA was restricted to pathways certified by the ASTM or under the official task force of the ASTM working toward certification in light of the study's emphasis on pathways anticipated to be commercially available in the near future. There are twelve such task forces, which represent six families of conversion technologies: Fischer-Tropsch (FT), direct sugars to hydrocarbons (DSHC), hydrotreated depolymerized cellulosic jet (HDCJ), alcohol to jet (ATJ), hydroprocessed esters and fatty acids (HEFA), catalytic hydro thermolysis (CT) and aqueous phase reforming (APR). Figure 5 summarises the feedstocks and critical processes for each of these. A number of other RJF pathways exist but have been excluded since ASTM task forces around these have yet to be formed [9].
Advancements in aviation/jet fuels
Currently, nonrenewable petroleum is the source of traditional jet fuel, and burning this fuel significantly raises atmospheric carbon dioxide levels and contributes to global warming. Furthermore, aromatic chemicals included in petroleum-based fuels have the potential to produce particles that heighten radiative forcing, leading to further effects on global warming. In response to these obstacles, scientists worldwide strive to create effective techniques for converting lignocellulosic biomass and even carbon dioxide into SAF that burns cleanly and performs well. Synthesis of fuel molecules from bio-based platform chemicals is one promising path toward SAF. Isoprene is one of the most sought-after and adaptable platform chemicals. Isoprenol and mesonic/itaconic acid are examples of other bio-based molecules from which this five-carbon conjugated hydrocarbon can be directly produced through fermentation. Isoprene is easily transformed into jet fuel blendstocks using oligomerisation reactions and catalytic and photochemical cycloadditions. The cycloalkanes prepared using these methods have low viscosities, high densities, and combustion temperatures.
While isoprene-derived discrete molecules make excellent blendstocks, conventional jet fuel is a complex blend of aromatic compounds with carbon numbers ranging from approximately 9 to 14, n-alkanes, isoalkanes, and cycloalkanes. Research is underway to create procedures that can transform isoprene into more expansive hydrocarbon distributions that resemble Jet-A's to enhance the role of isoprene as a precursor to jet fuel, as shown in Figure 6. It is necessary to use readily available bio-based molecules or mixtures combined with isoprene to achieve this goal while still producing SAF. The two most apparent options are syngas and ethanol [10].
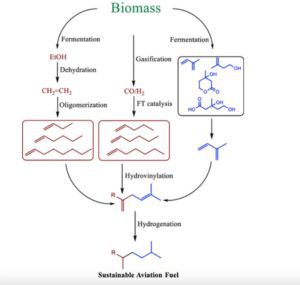
Figure 6: Synthesis of sustainable aviation fuels through hydroxylation of isoprene with mixed α-olefins [10].
Biofuels are becoming increasingly popular as a substitute for liquid fuel because of their renewable nature, advantageous chemical composition, and reduced lifecycle emissions. The production of SAF from biomass and leftover waste is the main topic of this review. Approximately 343 billion liters of aviation fuel were consumed annually before the COVID-19 pandemic, with only 0.015 billion liters coming from renewable sources [11]. By 2050, the aviation industry is expected to contribute 5% of global greenhouse gas emissions if business as usual continues [11].
The international airline sector has pledged to meet aggressive climate change goals, such as halving carbon dioxide emissions by 2050 and achieving carbon-neutral growth starting in 2020. Increasing the use of SAF is essential to achieving these goals. As of right now, the ASTM D7566 standard has approved five different production routes: HEFA fuels made from used cooking oil, animal fats, algae, and vegetable oils (like camelina), FT fuels using solid biomass resources (like wood residues), FT fuels with aromatics using solid biomass resources (like wood residues), Synthetic iso-paraffin (SIP) made from fermented hydro processed sugar, which can be blended up to 10% and Alcohol-to-jet (ATJ) fuels made from isobutanol, which can be blended up to 30% [11]. The routes are based on the five primary conversion techniques shown in Figure 7.
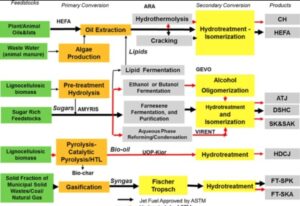
Figure 7: Approved and under investigation production pathway for biofuel synthesis [11].
Any carbonaceous material can be gasified, a thermochemical process that produces syngas, which is primarily carbon monoxide and hydrogen. This is one of the routes that uses waste feedstocks and solid biomass to synthesize drop-in aviation fuels. The most common method of gasification used in industry is autothermal, which involves reacting a sub-stoichiometric amount of oxygen with the carbonaceous feedstock at temperatures between 800 and 1200 °C. Biomass and residual wastes are promising feedstocks for synthetic aviation fuels because of their low carbon footprint and renewability. Still, they face challenges from low energy density and high composition variability [11]. The gasifying waste to produce chemicals and electricity has been reviewed recently. One hundred fourteen biomass gasification projects are operating globally, 15 are dormant or suspended, and 13 are in the planning or building stages. One hundred six of those plants are used to produce electricity, twenty-four are used to produce liquid fuel, eight are used to synthesize gaseous fuel, and the remaining seven are used to produce chemicals. Depending on the configuration, gasifiers are classified into three main types: fixed bed, fluidized bed, and entrained flow. These generic gasifiers can be further divided into categories shown in Figure 8
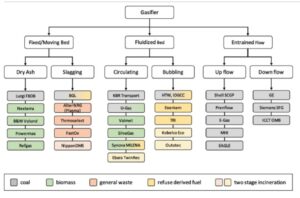
Figure 8: Classification of gasifiers and commercially available technologies by feedstock type [11].
Future of SAF and challenges
It has been challenging to reduce aviation greenhouse gas emissions through electrification because long-haul flights cannot be powered by current battery technology. Green hydrogen and other alternative fuels with reduced emissions are still in the early stages of development regarding aircraft engine production.
As a result, major airlines and the US government have shifted to using SAF, a fuel with a low to negative carbon intensity that is practically chemically and physically identical to conventional jet fuel. Refineries in the United States currently make most of the jet fuel used in airplanes. Each of the five Petroleum Administration for Defense Districts (PADDs) that comprise the United States has a different production-to-consumption ratio for jet fuel. Most PADDs, like PADD 5 on the East Coast, which generally produces less than 16% of its jet fuel, use more than they can generate. The one exception is PADD 3, which uses less than a third of its production capacity while producing more than 60% of the jet fuel used in the United States at refineries along the Gulf Coast [12]. As a result, PADD 3 primarily transports jet fuel out of it to make room for other PADDs with more frequent flights. However, BTU Analytics estimates that all of these facilities combined would only be able to produce around 2.1 billion gallons of SAF per year by 2030, falling short of the government’s 3-billion-gallon goal [12].
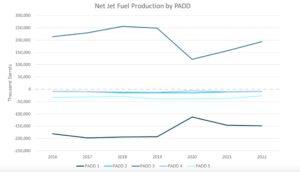
Figure 9: Net Jet Fuel Production by Petroleum Administration for Defense Districts [12].
While technical opportunities remain and new pathways are constantly emerging, the key challenges for commercial-scale SAF deployment include cost, supply chain development and risk management, and demonstration of sustainability. Although the selling prices of produced SAF are not public, SAF currently are more expensive than traditional jet fuel made from petroleum.
Given their current costs and competitive environment, many airlines are unwilling or unable to pay extra for SAF, making it difficult for them to absorb this cost differential and reduce their carbon footprint. Even though SAF's energy content is entirely interchangeable with conventional fuels, its environmental benefits from carbon reduction outweigh any drawbacks associated with traditional fuels.
They should be considered when evaluating their worth. Technoeconomic analysis (TEA) is a valuable technique for assessing the economic aspects influencing the selling price of fuel and finding areas where supply chain costs can be cut. Consistent TEAs for various options are valuable for comparing fuel production pathways. According to DOE targets, the US Department of Energy has created a set of biofuel TEAs that emphasise cost-cutting potential [13]. A second set of harmonized TEAs for the seven certified SAF pathways has been developed with uniform approaches to economics, finance, feedstock preparation, and support systems. The impact of federal and state policies that assess the environmental services offered by SAF has been assessed using these models. For real-world costs, as currently understood, researchers are implementing stochastic and deterministic TEA analysis assuming various policies and technology maturation rates to aid in thinking about uncertain future conditions [13]. Other researchers are analysing the influence of techno economics, technology maturation rates, and policies on deployment potential for SAF and other fuels.
Conclusion
The global aviation industry has been a rapidly expanding sector in recent years. One of the significant advances in SAF production has been the scaling up of production facilities. Several companies and governments have invested in expanding SAF's production capacity to meet the growing demand for airline services.
However, the critical challenges for commercial-scale SAF deployment include cost, supply chain development and risk management, and demonstration of sustainability. Techno-economic models have been used to evaluate the influence of federal and state policies that consider environmental services provided by SAF. For real-world costs, as currently understood, researchers are implementing stochastic and deterministic TEA analysis assuming various policies and technology maturation rates to aid in thinking about uncertain future conditions.
SAF could contribute around 65% of the reduction in emissions needed by aviation to reach net zero. This will require a massive increase in production to meet demand and engage with a wide range of industry and policy stakeholders on all SAF topics and, facilitate cooperation and promote partnerships between them, provide policy support at national, regional, and international levels to create the necessary framework for the commercialization of SAF, work towards removing barriers to the realization of a cost-competitive SAF market and promote the global harmonization of sustainability criteria for SAF.
References:
1. Developing sustainable aviation fuel (SAF). IATA. (n.d.-a). https://www.iata.org/en/programs/environment/sustainable-aviation-fuels/
2. Detsios, N., Theodoraki, S., Maragoudaki, L., Atsonios, K., Grammelis, P., & Orfanoudakis, N. G. (2023). Recent Advances on Alternative Aviation Fuels/Pathways: A Critical Review. Energies, 16(4), 1904. https://doi.org/10.3390/en16041904
3. Air bp. (n.d.). How all sustainable aviation fuel (SAF) feedstocks and Production Technologies can play a role in decarbonizing aviation: News and Views. Air bp. https://www.bp.com/en/global/air-bp/news-and-views/views/how_all_sustainable_aviation_fuel_SAF_feedstocks_and_production_technologies_can_play_a_role_in_decarbonising_aviation.html
4. Sustainable aviation fuel. Alternative Fuels Data Center: Sustainable Aviation Fuel. (n.d.). https://afdc.energy.gov/fuels/sustainable_aviation_fuel.html
5. Our commitment is to fly net zero by 2050. IATA. (n.d.-b). https://www.iata.org/en/programs/environment/flynetzero/
6. Office, U. S. G. A. (n.d.). Sustainable aviation fuel: Agencies should track progress toward ambitious federal goals [reissued with revisions May 17, 2023]. Sustainable Aviation Fuel: Agencies Should Track Progress Toward Ambitious Federal Goals [Reissued with Revisions May 17, 2023] | U.S. GAO. https://www.gao.gov/products/gao-23-105300#:~:text=SAF%20production%20and%20use%20in,U.S.%20airlines%20(see%20table).
7.11.Net zero 2050: Sustainable aviation fuels. (n.d.). https://www.iata.org/en/iata-repository/pressroom/fact-sheets/fact-sheet---alternative-fuels/?ref=benchmark. money
8. Kramer, S., Andac, G., Heyne, J., Ellsworth, J., Herzig, P., & Lewis, K. C. (2022). Perspectives on Fully Synthesized Sustainable Aviation Fuels: Direction and Opportunities. Frontiers in Energy Research, 9, 782823. https://doi.org/10.3389/fenrg.2021.782823
9.Mawhood, R., Gazis, E., Hoefnagels, R., & Slade, R. (2016). Production pathways for renewable jet fuel: A review of commercialization status and future prospects. Biofuels, Bioproducts and Biorefining, 10(4), 462-484. https://doi.org/10.1002/bbb.1644
10. Designer Biosynthetic Jet Fuels Derived from Isoprene and α-Olefins
C. Luke Keller, Christopher J. Walkling, Derek D. Zhang, Lawrence C. Baldwin, Jessica S. Austin, and Benjamin G. Harvey
ACS Sustainable Chemistry & Engineering 2023 11 (10), 4030-4039
DOI: 10.1021/acssuschemeng.2c05297
11. Shahabuddin, M., Alam, M. T., Krishna, B. B., Bhaskar, T., & Perkins, G. (2020). A review on producing renewable aviation fuels from the gasification of biomass and residual wastes. Bioresource Technology, 312, 123596. https://doi.org/10.1016/j.biortech.2020.123596
12. The Future of Sustainable Aviation Fuel Production in the U.S. BTU Analytics. (2023, January 18). https://btuanalytics.com/energy-transition/the-future-of-sustainable-aviation-fuel-production-in-the-u-s/#:~:text=In%20September%202021%2C%20the%20Biden,by%202030%20and%202050%2C%20respectively.
13. Lewis, K. C., Brown, N. L., Goldner, W. R., Haq, Z., Hoard, S., Holladay, J. E., & Wolcott, M. P. (2022). Editorial: The motivations for and the value proposition of sustainable aviation fuels. Frontiers in Energy Research, 10, 1005493. https://doi.org/10.3389/fenrg.2022.1005493
Dr Raj Shah is a director at Koehler Instrument Company in New York, where he has worked for the last 28 years. More information on Raj can be found at https://bit.ly/3QvfaLX
Contact: rshah@koehlerinstrument.com
Ms. Salowa Siddique is part of a thriving internship program at Koehler Instrument company in Holtsville, and are students of Chemical Engineering at Stony Brook university, Long Island, NY where Dr Shah and Mittal are on the external advisory board of directors.
Dr Vikram Mittal, is an associate professor at the United States Military Academy in the Department of Systems Engineering. He earned his doctorate in Mechanical Engineering at the Massachusetts Institute of Technology where he researched the relevancy of the octane number in modern engines. His current research interests include various energy technologies, system design, model-based systems engineering and modern engine technologies. He has numerous publications in various peer reviewed journals.